As a pivotal component in the realm of high technology, semiconductor foundries have exacting requirements for ultra-pure water. Amidst these stringent demands, SJ Gauge's team, drawing upon years of experience and specialized knowledge, has customized high-quality switch contact differential pressure gauges to ensure the precision and stability of ultra-pure water filtration. This case study not only symbolizes the fusion of technology and innovation but also exemplifies the guiding principle of the SJ Gauge brand: providing the best solutions for our customers. We firmly believe that every success emanates from collective teamwork and an unwavering commitment to quality and excellence.
In the forthcoming case study, we will delve deeper into the intricacies of these optimal solutions and share how SJ Gauge's professional support facilitates the realization of customer needs and goals. Stay tuned as we continue to explore this journey filled with challenges and accomplishments together.
#01Client background
As one of the world's top ten semiconductor foundries, PSMC not only serves as the designated partner for many IC distributors but also handles the foundry services for many LCD panel manufacturers. Within the whole semiconductor industry chain, PSMC plays a crucial role as a key producer.
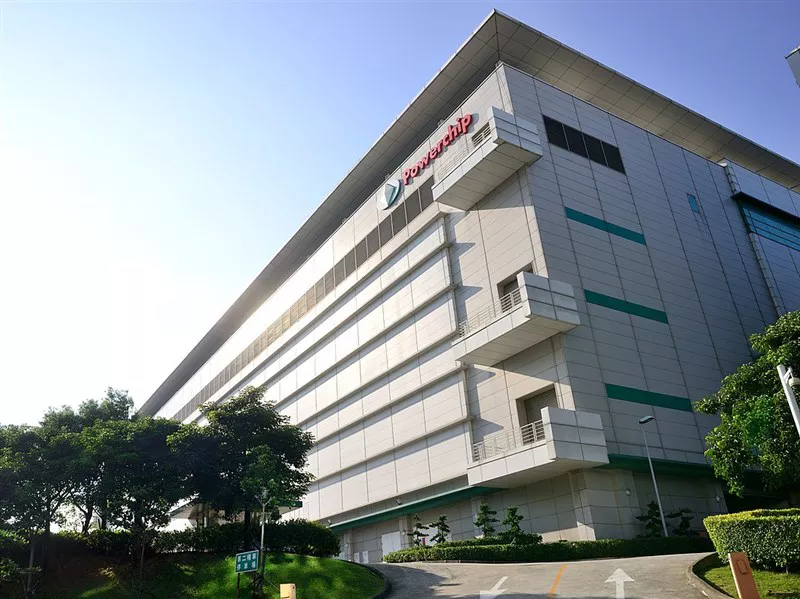
#02Challenge
In the manufacturing process of semiconductor wafers, it's necessary to use ultrapure water to rinse away contaminants from the wafers.
The wastewater generated from the manufacturing process also needs to pass through multiple filtration systems before being discharged from the factory. Therefore, periodic replacement of filter cartridges has become an essential part of quality control. Differential pressure gauges help operators evaluate the cleanliness of the filter cartridges. When the pressure difference between the two ends exceeds a certain value, it indicates that the filter cartridge is clogged and needs to be replaced immediately.
After years of use, the differential pressure gauge must be repaired and maintained more frequently. Since the warranty period had already expired, and waiting for the original manufacturer to make repairs took too long, PSMC decided to seek another supplier.
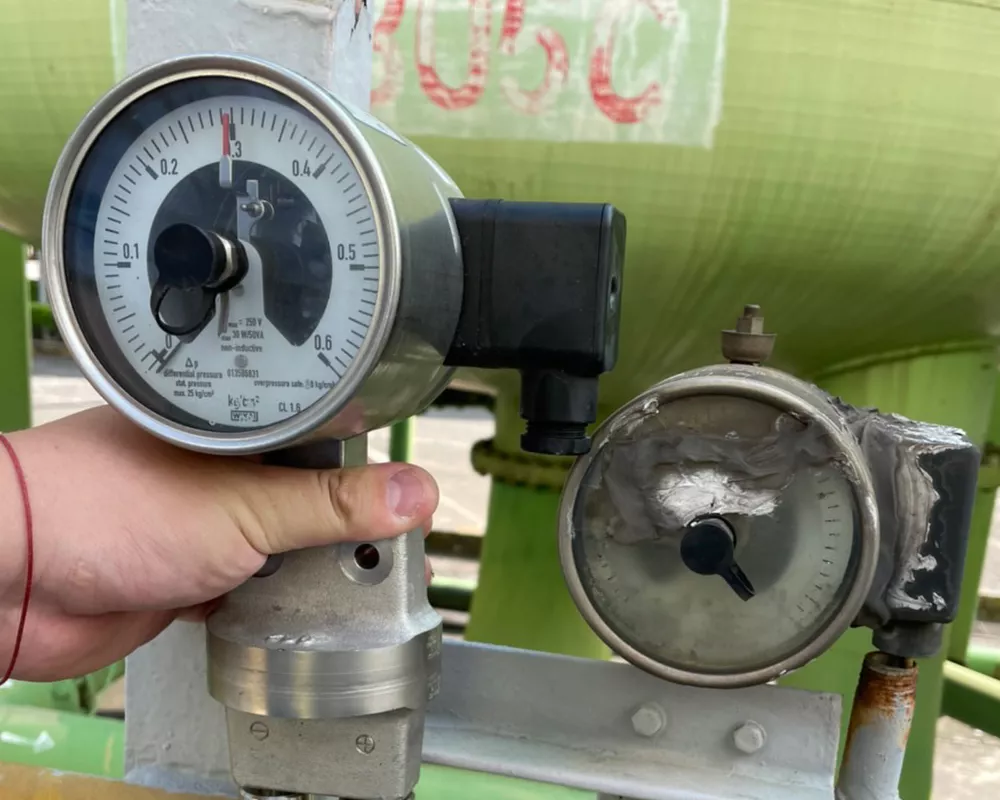
#03Client demand
- To ensure the best production quality, the customer needed a differential pressure gauge to measure whether the filter cartridge needs to be replaced.
- The customer expects that when the differential pressure value exceeds the preset range, the switch will turn on and will trigger the alarm automatically to notify operators.
- When the pressure sources of both ends are connected, the differential pressure value may be unstable initially. The customer needed to install a protective device to avoid instrument damage from excessive differential pressure values.
#04Solutions and client feedback
SJ Gauge's PRBD Bellow Tube Differential Pressure Gauge measures the pressure value of both ends through its internal sensing components.
The differential pressure value helps operators evaluate the cleanliness of the filter cartridge to determine whether it needs to be replaced.
In order to help the customer to reduce labor costs, SJ Gauge has installed a switch contact. When the differential pressure value exceeds the
preset range, the switch contact will make the circuit and trigger the alarm automatically, notifying operators to replace the filter cartridge
and ensure the system functions properly.
SJ_Differential%20pressure_gauge_eletric_contact
To avoid damage to the instruments, SJ Gauge provided a PRA-VS Valve Manifold as a solution. PRA-VS consists of two types of valves,
a shut-off valve and a pressure compensating valve. Shut-off valves can separate the process media from the differential pressure gauge,
allowing operators to dismount instruments during operation. Pressure-compensating valves can balance pressure at both ends to avoid
one-sided overpressure during commissioning and operating.
SJ Gauge also provided a selection of five-valve manifolds, which are equipped with two additional vent valves,
allowing operators to vent one or both pressure sides, or to clean the instrument.
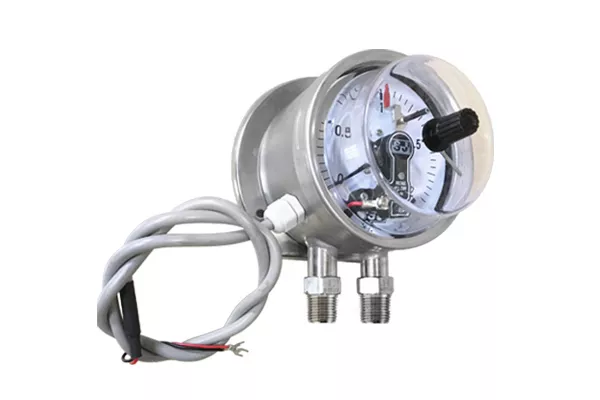
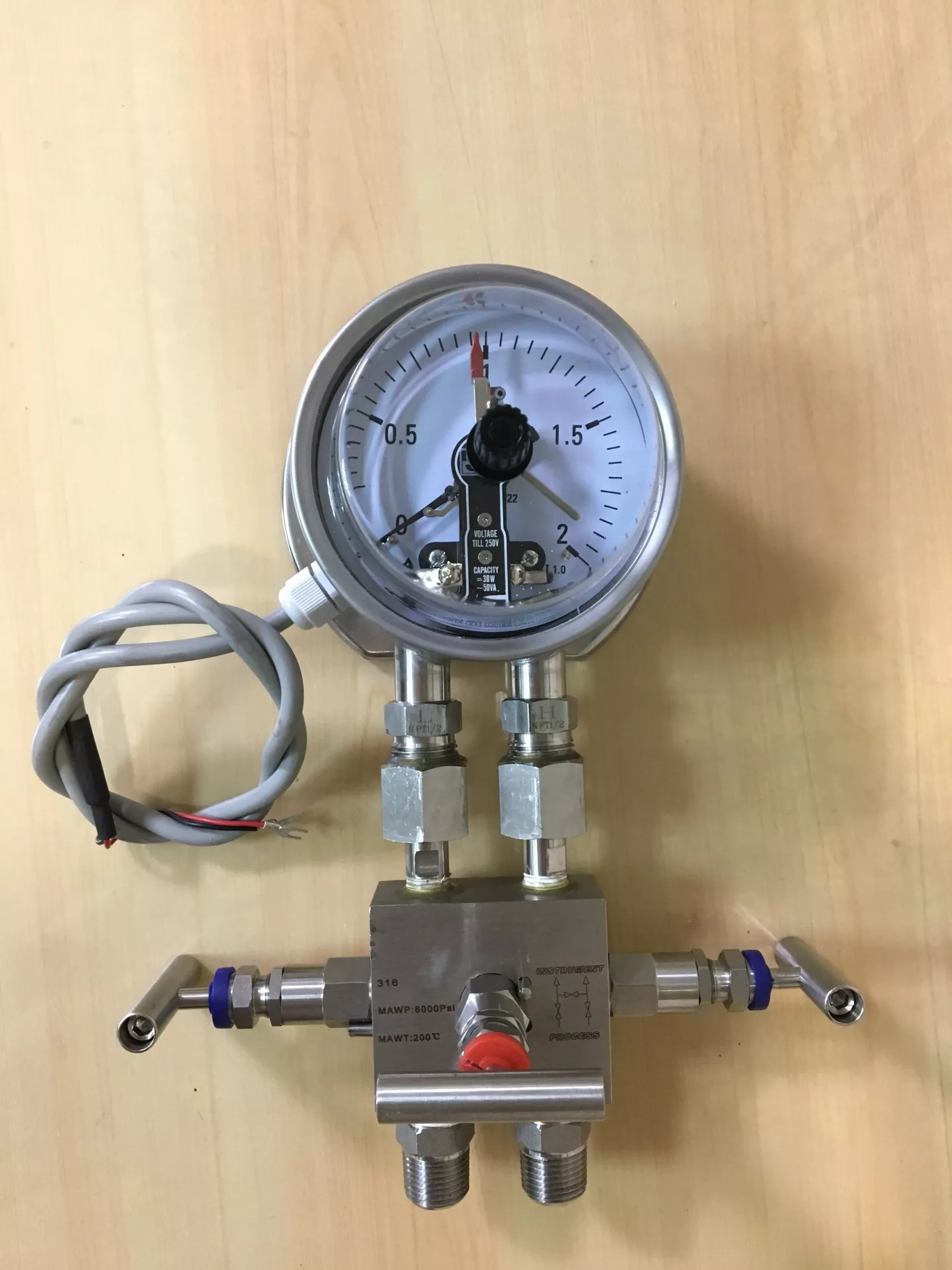
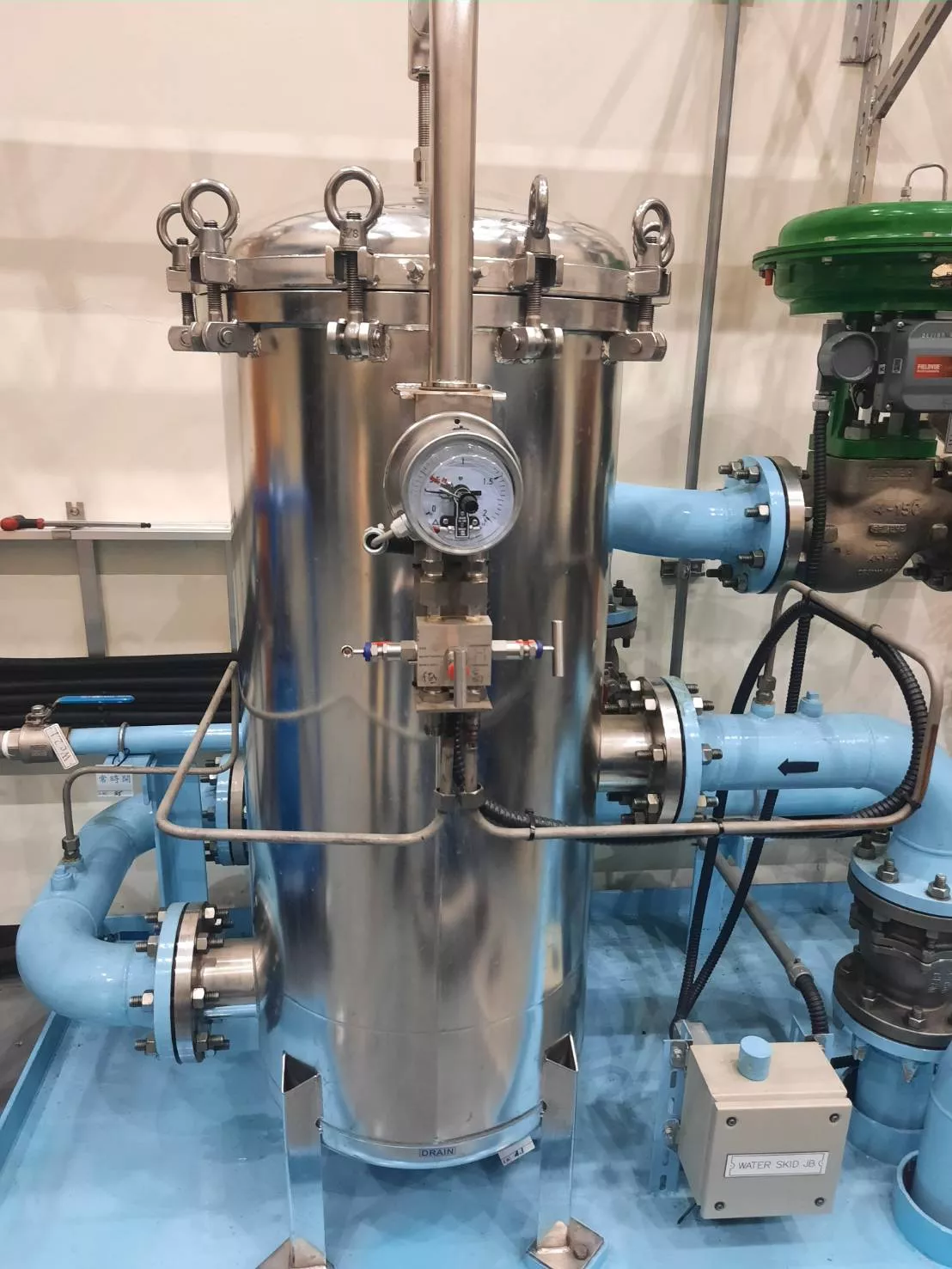
Our solution helped our client achieve multiple goals, including determining whether the filter cartridges need to be replaced, maintaining the best production quality, reducing labor cost and ensuring the system functions properly. We also met the short delivery time set by the client.
SJ Gauge provided product warranties and maintenance services, and we continue to ensure that our client receives prompt after-sales services.